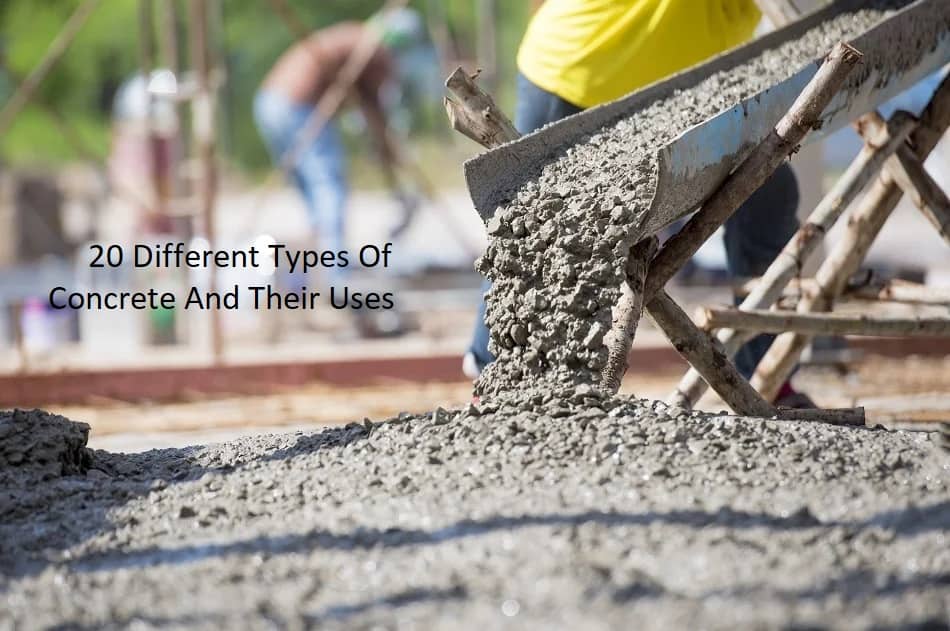
Concrete is present almost everywhere you look, bridges, buildings, walls, roadways, swimming pools, floors, airport runways, patios, and even a cement house. All these structures are depending on a man-made material with a super-easy formula: concrete.
Concrete is made of water, coarse aggregates, and cement. All three items are mixed to make a construction material that will harden over time. The properties of concrete depend on how much cement and water you mix. These properties are:
- Durability
- Strength
- Workability
- Resistance to radiation or heat
Fresh concrete has several applications and it can be cast into rectangles, circles, squares, and different other shapes. Concrete is also used to construct columns, staircases, beams, lentils, doors, and similar structures. It comes in different grades such as high strength, standard, and normal. The grades are used to indicate the strength of the concrete and how it should be applied to construction.
To determine what kind of concrete you should opt for, read on to find out the different types of concrete available in the market. But before that let’s learn how concrete is made.
Making Of Concrete
Regardless of the purpose of the concrete, you must make sure that you mix in the right proportions when you make concrete. There are two different mixes to make concrete.
- Nominal mix
- Design mix
1. Nominal Mix
The nominal mix is used for the most ordinary construction such as residential buildings. This mix mostly makes use of 1:2:4 proportion, i.e., one part of cement to two parts of sand and four parts of aggregate.
2. Design Mix
The design mix is also called the mix design and consists of proportions that are finalized using lab tests run to determine the strength of the mixture. This mix determines the strength you require by analyzing the structural design of the concrete component.
There are also various types of mixing methods apart from the classification of the mixing proportions. If you are confused over which type of mixing methods to choose, then consider the quality and quantity of the concrete you need.
A. Machine mixing
B. Hand mixing
A. Machine Mixing
There are different types of machines available to mix concrete. The collected ingredients are put into these machines and mixed and you get fresh concrete.
B. Hand Mixing
The ingredients are put on a flat surface and mixed by hand. Then the required amount of water is added little by little and mixed using special tools designed specifically for hand mixing.
22 Types Of Concrete
Let’s check out how many types of concrete are available. Some of these different types of concrete are used for the same purpose but have different names because of their composition. What you choose depends on what you want to achieve with the concrete. Read on to know more!
- Normal strength concrete
- Ordinary or plain concrete
- Prestressed concrete
- Reinforced concrete
- Lightweight concrete
- Precast concrete
- High-density concrete
- Ready-mix concrete
- Air entrained concrete
- Volumetric concrete
- Decorative concrete
- Rapid set concrete
- Smart concrete
- Pervious concrete
- Limrecrate
- Roll compacted concrete
- Glass concrete
- Pumped concrete
- Asphalt concrete
- Shotcrete concrete
- High-strength Concrete
- High-Performance Concrete
Let’s dive deeper into what each type of concrete is and how you can differentiate between each type.
1. Normal Strength Concrete

Normal strength concrete has all the basic ingredients: aggregate, sand, and cement in the ratio of 1:2:4. It takes about 30 to 90 minutes for the ingredients to set in. However, the setting time varies concerning the weather conditions at the concrete site and also the properties of the cement. Normal strength concrete is used for buildings or pavements that do not require high tensile strength. It however cannot withstand stress created by vibrations or wind loading so it may not be appropriate for certain structures. Normal strength concrete has a compressive strength of 20 to 40 MPa.
2. Ordinary Or Plain Concrete
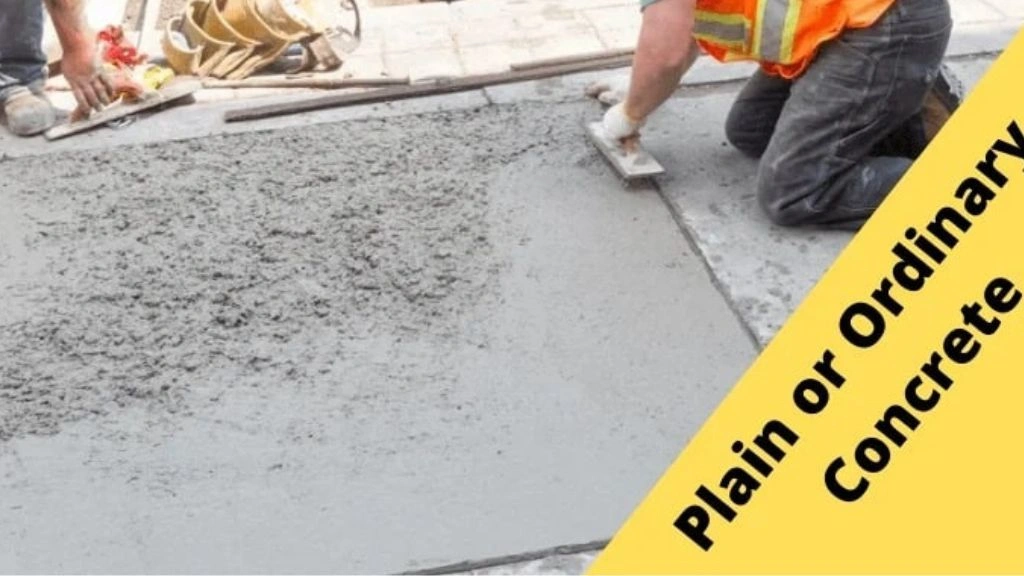
Plain or ordinary concrete is also used for buildings or pavements that do not require much tensile strength. It has a common mix of 1:2:4 ratio of cement, sand, and aggregate similar to normal strength concrete. So it also faces challenges similar to normal strength concrete such as not being ideal for withstanding wind loading or vibrations. However, plain or ordinary concrete is used for the construction of dams as the durability of this concrete is satisfactory. Plain concrete does not have steel reinforcing wires or bars. They have only two-tenths of 1 percent reinforcing.
3. Reinforced Concrete ( Rebar)
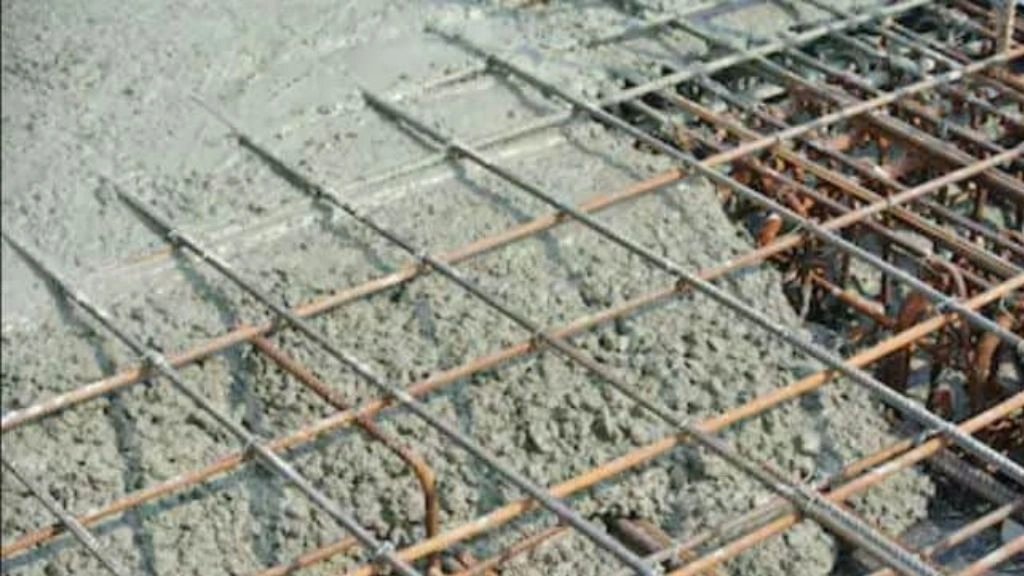
Reinforced concrete is used in modern and industrial buildings. It gains strength by the addition of cables, steel rods, and wires in the concrete before it has set in. Its common name is rebar and lately, fibers have been used to reinforce the concrete. The reinforcements resist the tensile forces and the concrete resists the compressive forces and together they create a strong bond that stabilizes a single structural element. Reinforced concrete was invented in the 19th century and led to a dramatic revolution in the construction industry. Roadways, buildings, and bridges all rely heavily on this type of concrete.
4. Prestressed concrete
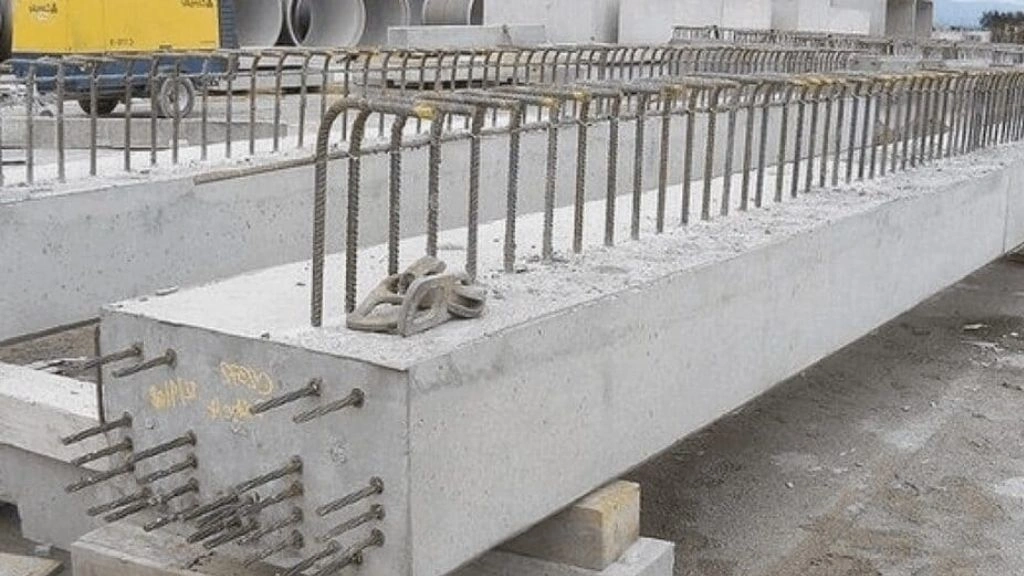
Pre-stressed concrete as the name suggests has tendons or bars that have been stressed beforehand and then incorporated into the concrete. It is used in many large projects such as roofs with a long span or other heavy load structures. The concrete is mixed and the bars are placed at the end of the structural units. It was first used in the late 19th century and now includes post-tensioning too (i.e., tensioning after the concrete has been cast). Making prestressed concrete requires skilled labor and heavy equipment. This concrete is usually prestressed and then assembled on site.
5. Precast concrete
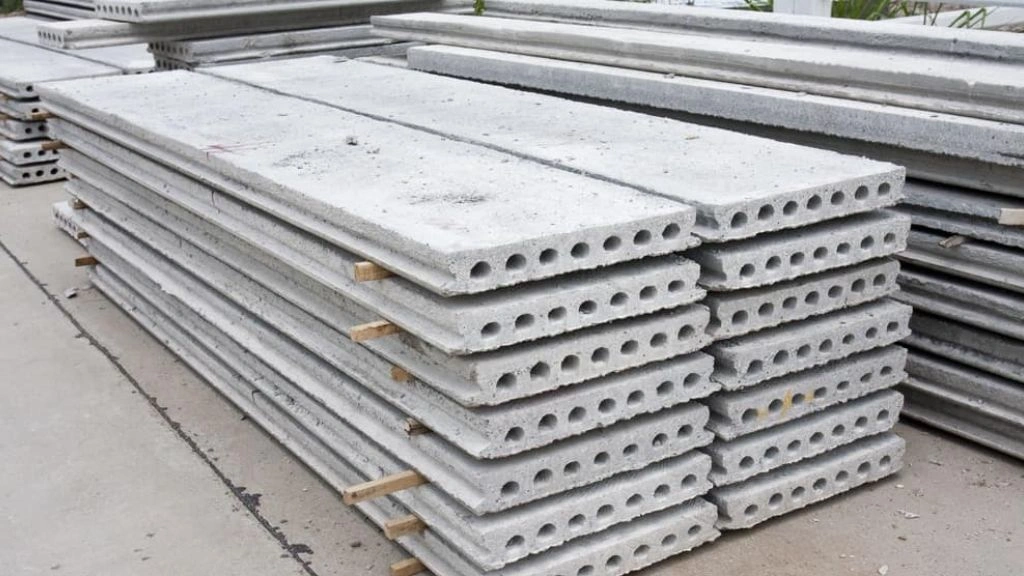
Taking exact specifications, precast concrete is made and cast in a factory and brought to the site to assemble. Since it is cast and cured in a precast plant, it has the opportunity to cure properly and be inspected by the plant employees. This concrete is used to make
- Concrete blocks
- Precast wall
- Poles
- Staircase units
The production of precast concrete is performed on the ground level making it cheaper as these forms can be reused many times before they are replaced. Onsite casting would be more expensive when you look at the cost per unit of formwork.
6. Lightweight concrete
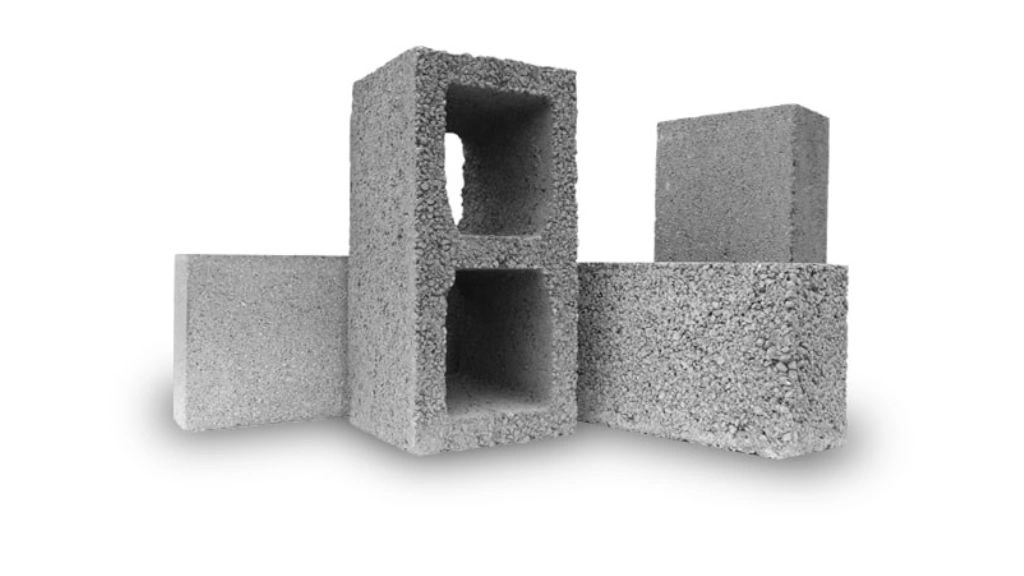
Any concrete with a density less than 1920 kg/㎥ is called lightweight concrete. It is created by mixing lightweight aggregates including natural materials such as pumice or scoria, artificial materials such as expanded shales and clays, or processed materials such as perlite and vermiculite. The most important property of lightweight concrete is that its thermal conductivity is very low. This concrete is commonly used in creating building blocks or long-spanning bridge decks and to protect steel structures.
7. High-density concrete
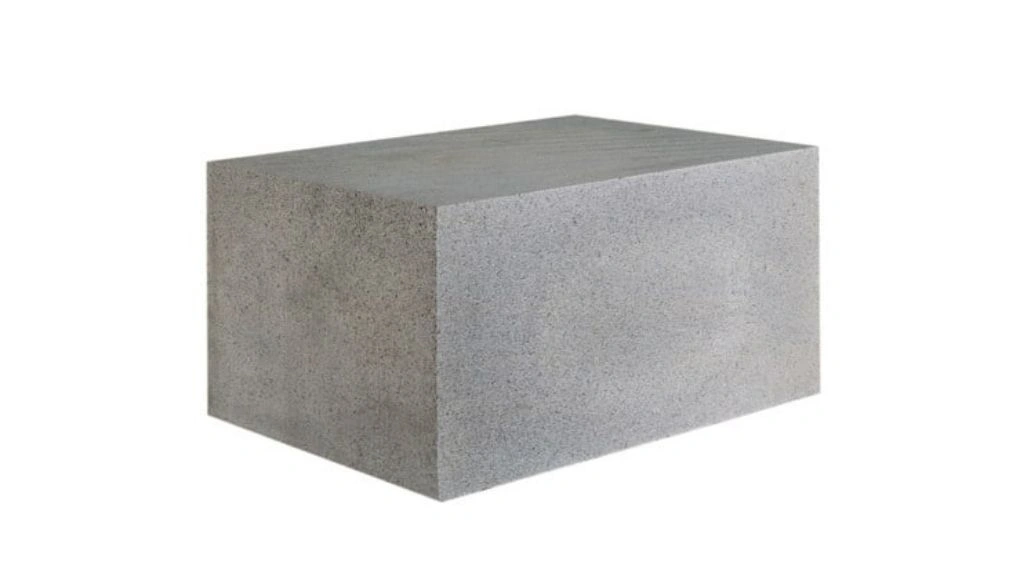
High-density concrete is specifically used in atomic power plants and is created by heavyweight aggregates that resist radiation. Crushed rocks are another component that is used in making high-density concrete. More specifically speaking, barytes which is a colorless, white material consisting of barium sulfate is the crushed rock that is most often used.
8. Air entrained concrete
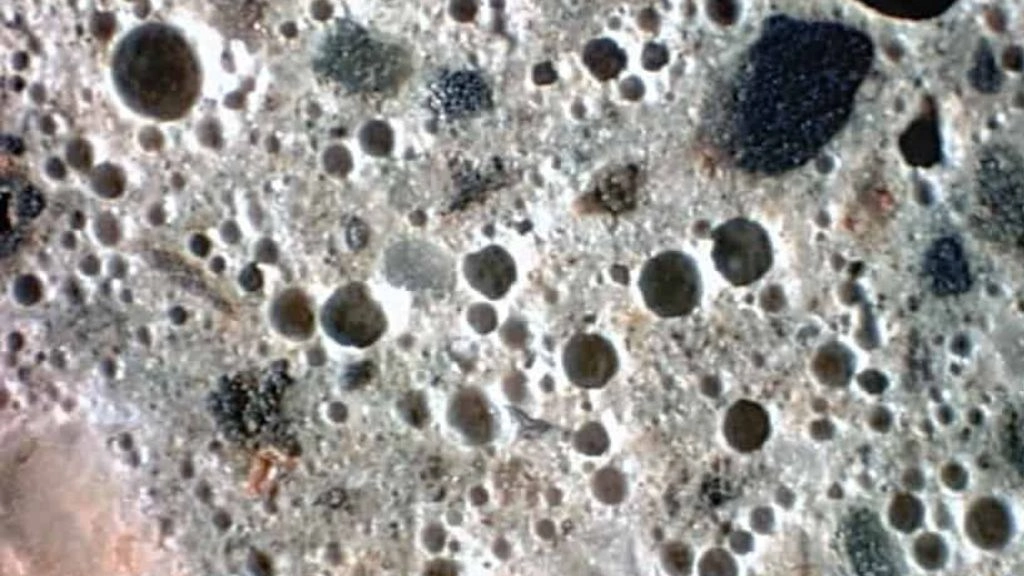
This type of concrete has billions of microscopic air cells every cubic foot. These air pockets relieve the internal pressure present inside the concrete. They also act as tiny chambers for water to expand into when they freeze. These air pockets are entrained inside the concrete by adding different foaming agents such as fatty acids, resins, or alcohols during mixing. These agents are incorporated under careful supervision by the engineers and add up to 3 to 6 percent of the total volume of the concrete. All the concrete used in areas with freeze-thaw cycles or freezing environments is air-entrained.
9. Ready-mix concrete
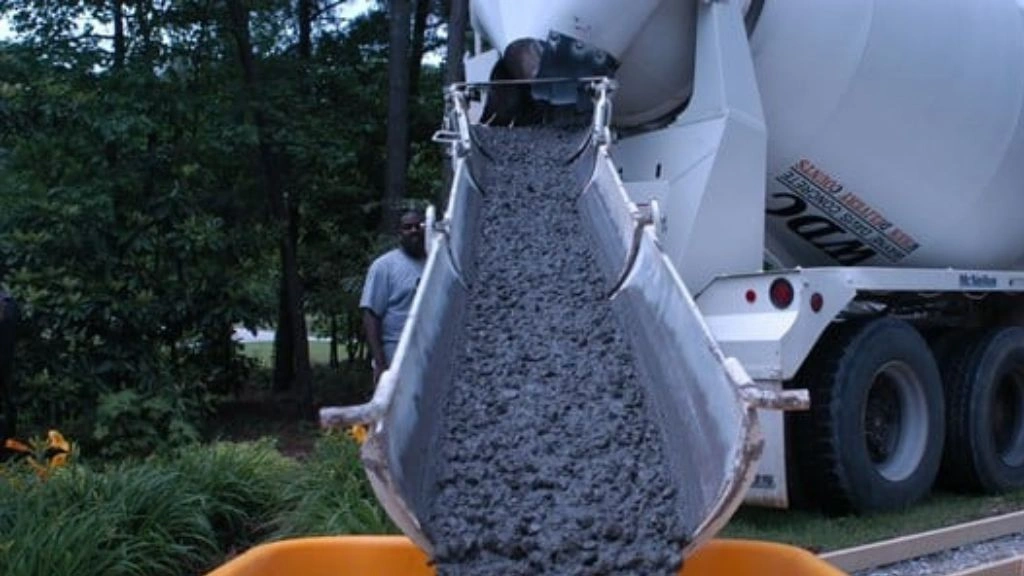
Ready-mix concrete is prepared and cured in a centrally located plant. It is mixed as it is being transported to the site. Once at the worksite, the concrete can be immediately used as no further treatment is required. Creating ready mix concrete needs a centralized location at an adjustable distance from the actual worksite. The concrete should not reach the worksite too late as then it would be useless as it would be set by a given time. To prevent the untimely setting of the concrete certain retarding agents are added. Ready-to-mix concrete is preferred over the concrete mixed on-site as they have high precision proportions and mixing. This concrete is used in the construction of walls, roadways, buildings, and many such structures.
10. Volumetric concrete
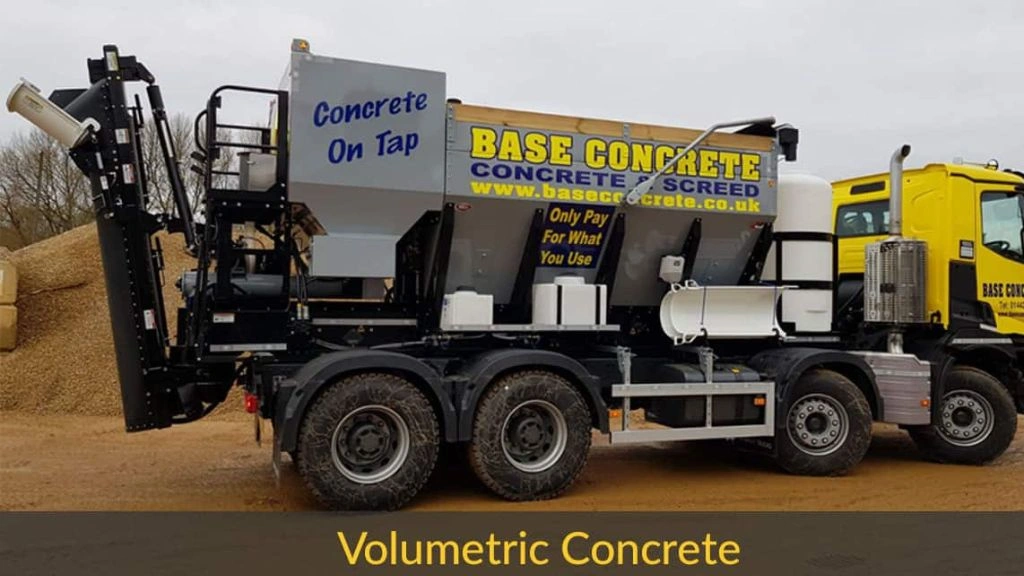
Volumetric concrete is an alternative to ready mix concrete developed to solve the issue of long-distance worksites. Ready-mix concrete tends to set in if the construction site and plant are set at a distance. But volumetric concrete is carried to the worksite in large volumetric mobile mixers at the construction site. These mixers carry aggregates, concrete, and water to be mixed at the worksite. This concrete is useful when the worker requires two different concretes to be mixed allowing one truck to produce two different mixes of concrete. It becomes very useful in multi-projects, basement constructions, and large sites.
11. Decorative concrete
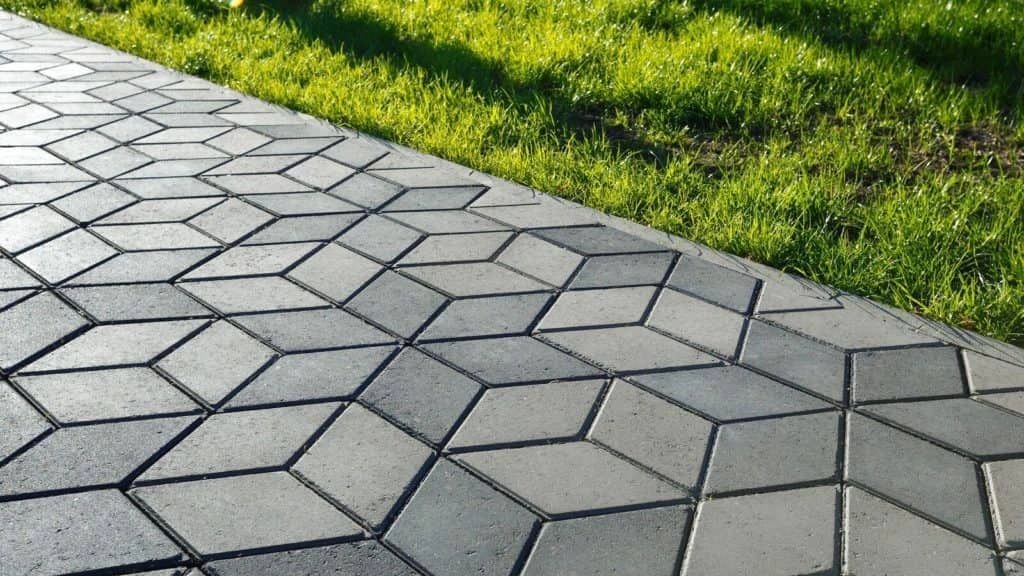
Decorative concrete is aesthetically and visually appealing and can go through different processes such as,
- Coloring
- Molding
- Polishing
- Etching
- Application of decorative toppings
It will add a touch of “personality” to the dull structures or surfaces. For instance, flooring and swimming pools can have an aesthetic statement through decorative concrete.
12. Rapid set concrete
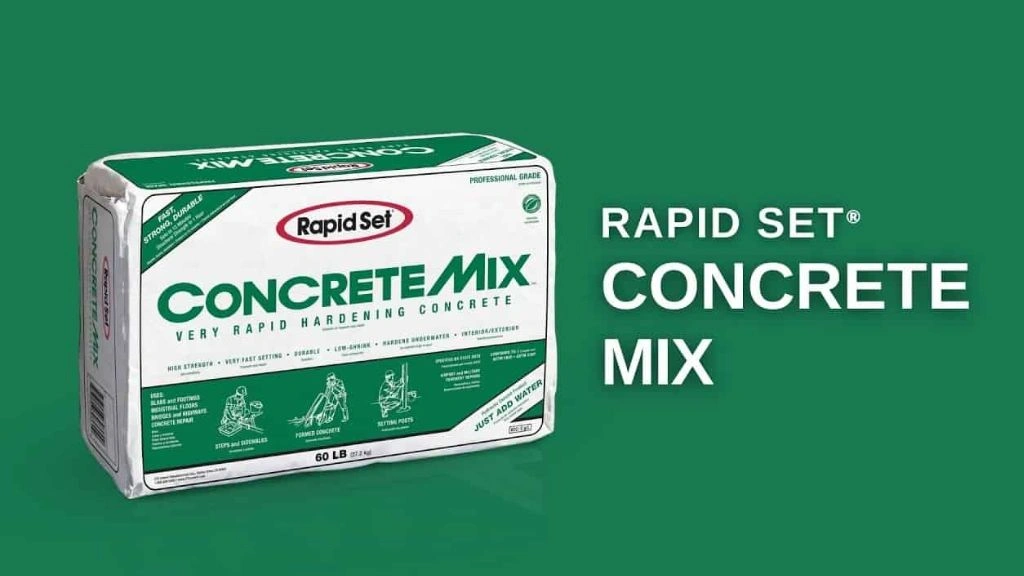
Rapid set concrete is ideal when you are short on time at the construction site. It sets fast and is extremely resistant to low temperatures which is why it can be used at all times of the year. During winter cold temperatures can prevent normal concrete to set in which is when rapid set concrete comes into the picture.
13. Smart concrete
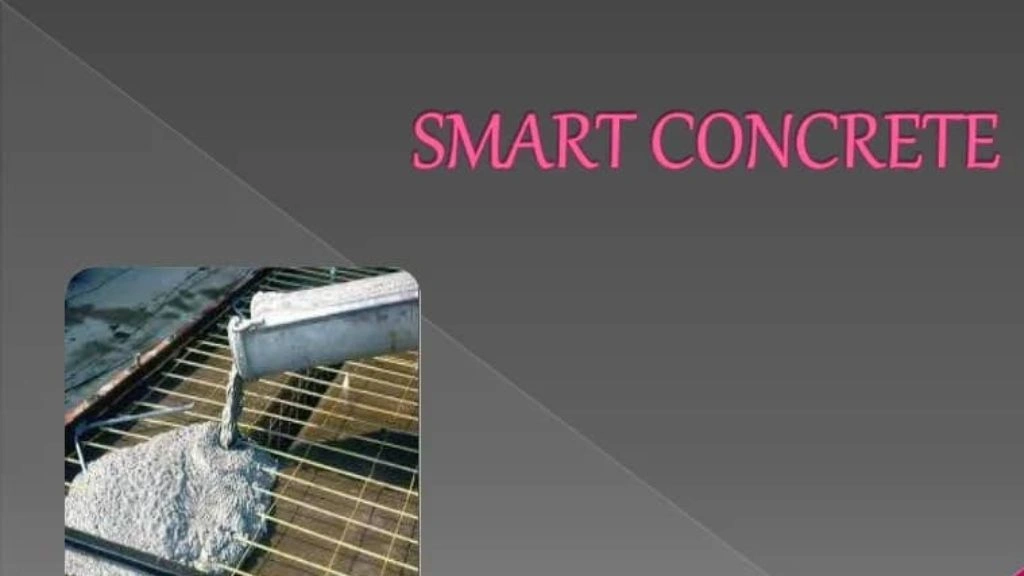
Smart concrete has short carbon fibers added to it by conventional concrete mixers which affect the concrete’s electrical resistance. This way it can withstand stress and strain and can be used to detect and monitor the condition of the reinforced concrete structures and prevent its subsequent failure. Even tiny structural flaws do not escape its detection. Smart concrete is not widely available but it is the future of concrete buildings that can even face a repeated earthquake risk.
14. Pervious concrete
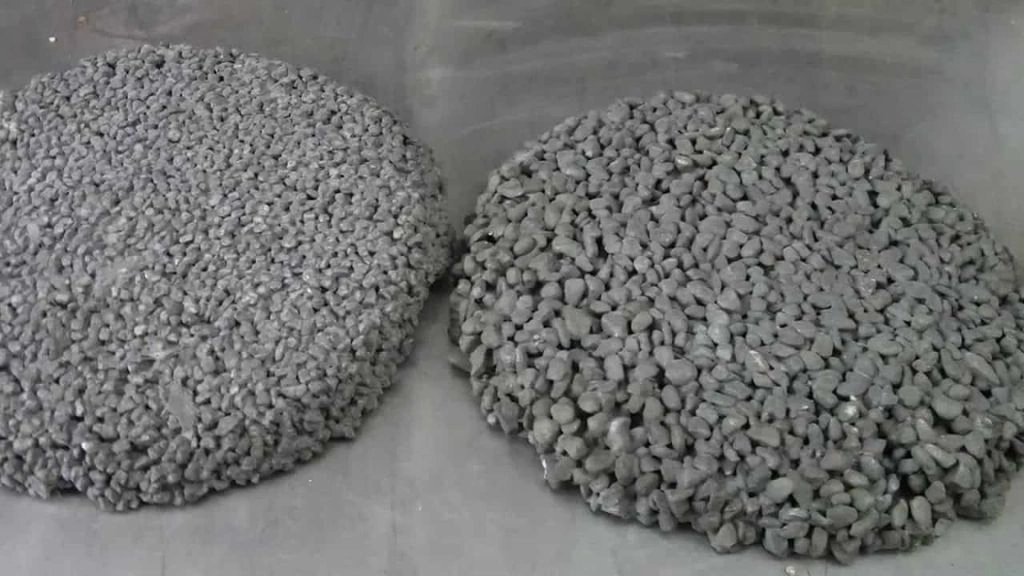
Pervious concrete has been designed to deal with issues caused by stormwater runoff, pools of water, and puddles on airport runways or roadways. They have superb hydroplaning ideas, snow buildup, and tire spray and obviates the need for storm sewers and curbing as they have super water-absorbing properties. It is made of coarse aggregate, water, and cement and contains no sand so an open scale and porous structure are created that allows water to pass through.
15. Limrecrate
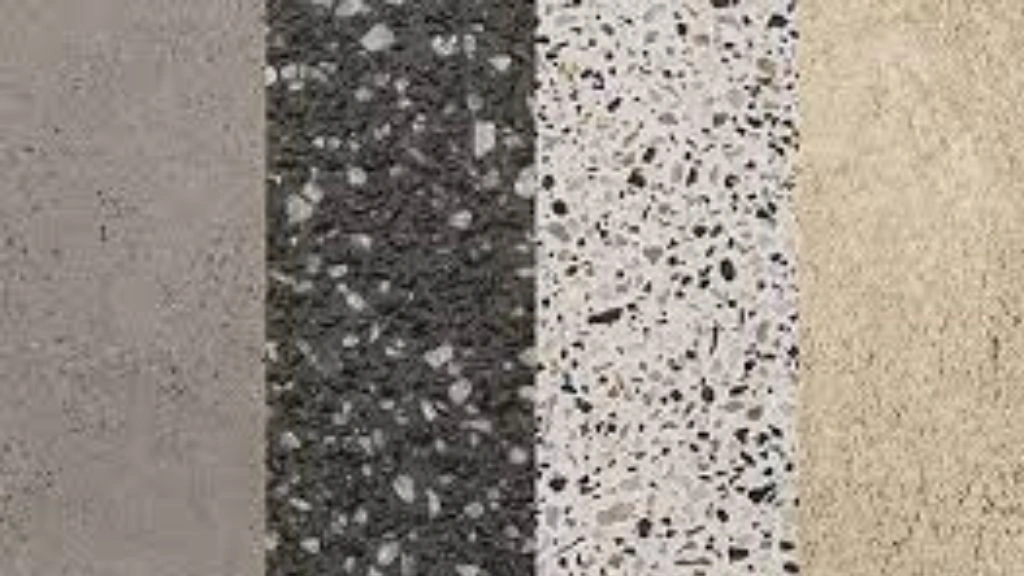
Limrecrate is named so because it used lime instead of cement in its making. The lightweight aggregates used in it are either sharp sand or glass fiber and it is used to construct domes, vaults, and floors. It can have many environmental benefits such as easy-clean, renewability, and use with radiant floor heating.
16. Roll compacted concrete
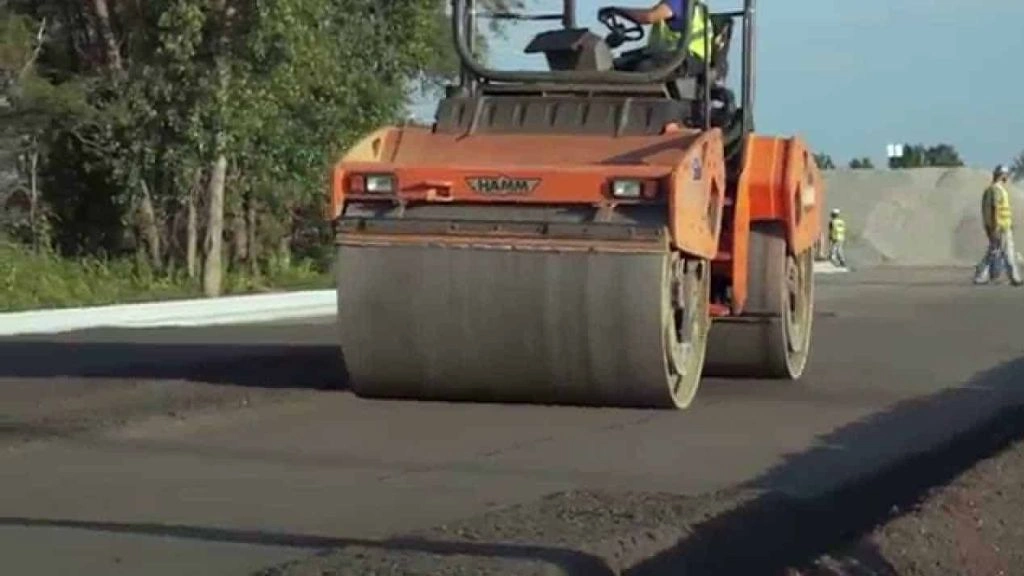
Roll compacted concrete is a familiar sight on American highways. It is a strong and dense concrete used in highways with heavy traffic of vehicles carrying heavy loads. This concrete emits fewer emissions during its production which makes it environment friendly. It can be found in industrial servicing, pavements, car parks, airport runways, and roadworks.
17. Glass concrete
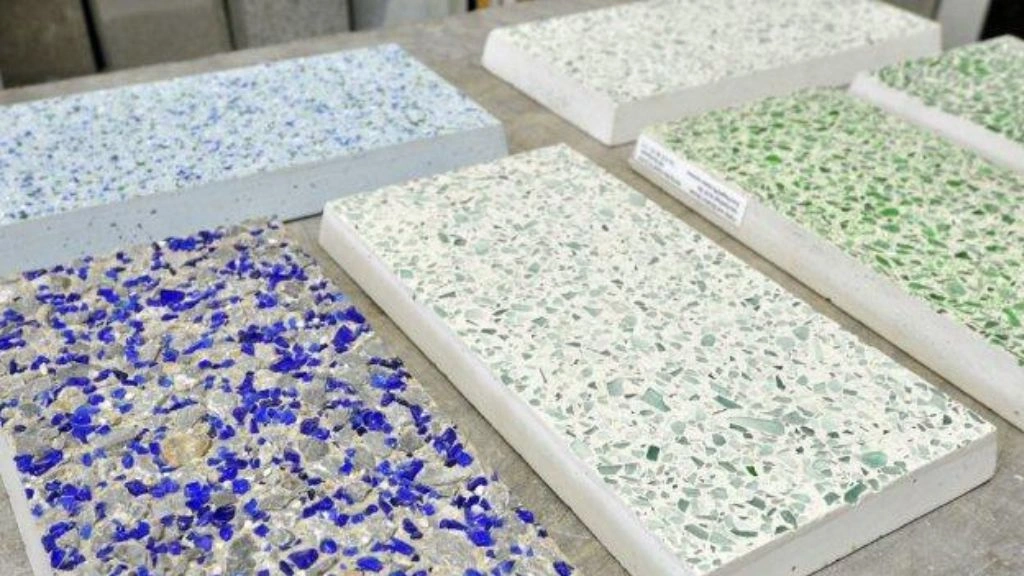
Glass concrete uses recycled glass and is used for aesthetic appeal. It is commonly used in large format slabs found on flooring and decorative facades and has shiny or colored glass embedded in it during the mixing process. This embedded glass gives it a distinctive sparkle.
18. Pumped concrete
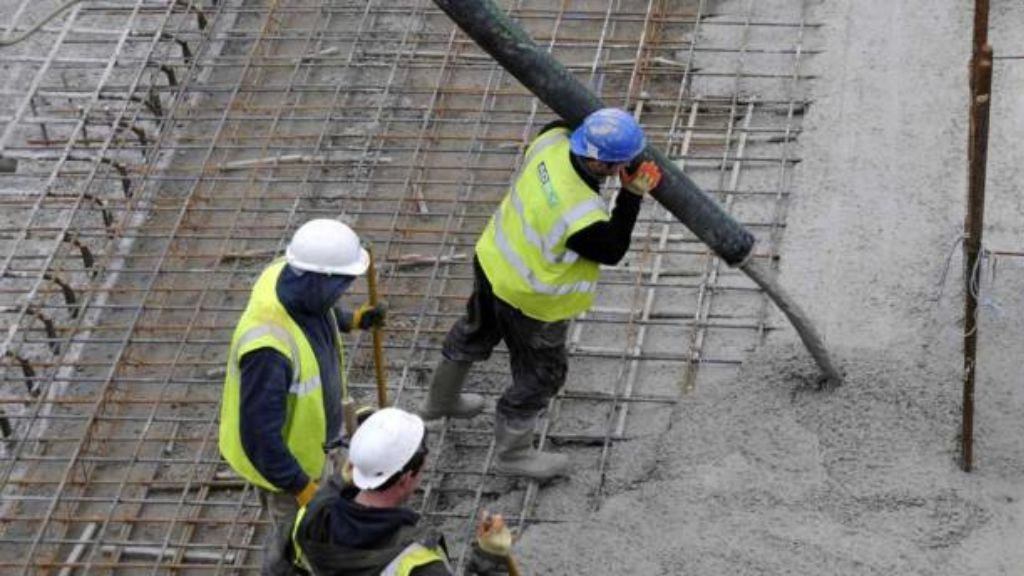
Pumped concrete is used to floor extremely tall buildings as it is very workable. It can be very easily conveyed via a pipe to the upper floors. This pipe must be a flexible one or a rigid hose so that concrete can discharge to the required area. Pumped concrete is used,
- To make super flat floors on low structures
- In the construction of bridges and roadways
- To construct swimming pools
Pumped concrete is reliable, economical, and efficient as very fine aggregates are used in its making. The finer the aggregate, the freer the flow of the concrete through the pipe.
19. Asphalt concrete
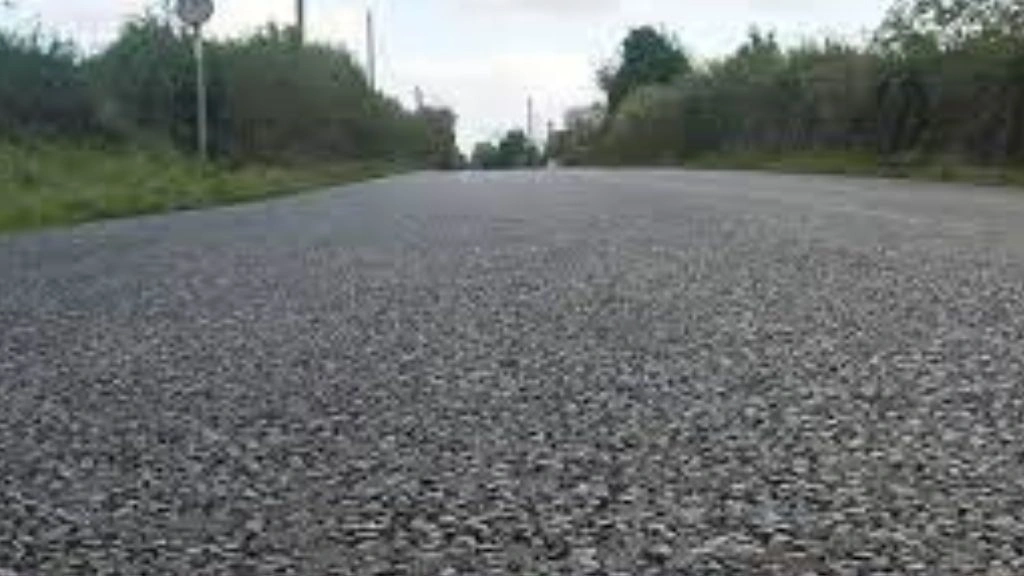
Asphalt concrete is also known as blacktop which is commonly used on roadways, airport runways, highways, parking lots, sidewalks among others. Asphalt is composed of dark minerals consisting of hydrocarbons called bitumens. The need for asphalt grew with the growth of the automobile industry and kept growing due to its permeability, flexibility, fatigue resistance, stability, skid resistance, workability, and durability. Asphalt and aggregate are their main constituents.
20. Shotcrete concrete
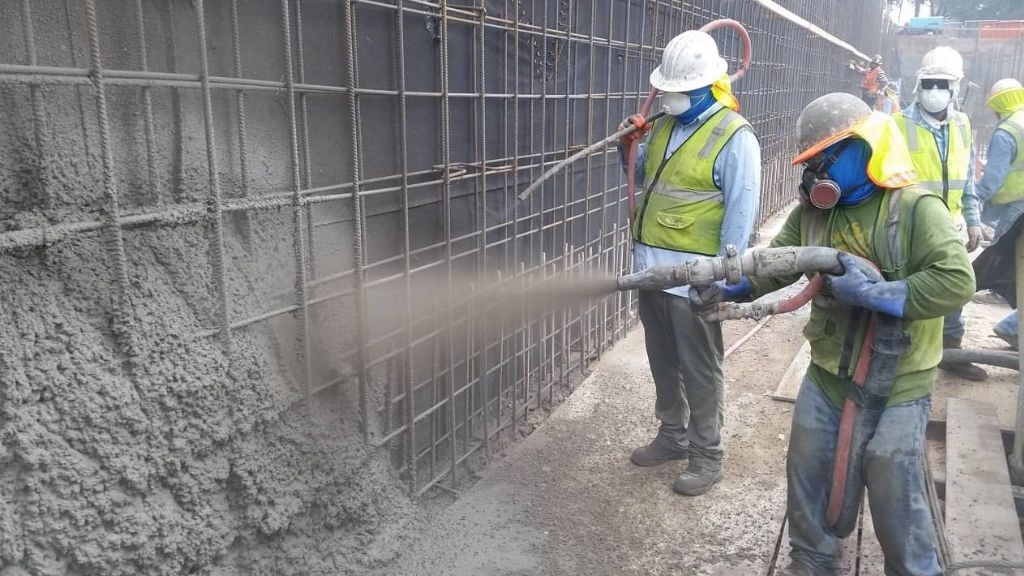
Shotcrete concrete is different compared to the other concrete especially in the way it is applied. It is shot through a nozzle with high air pressure onto a formwork or frame. The compaction of the concrete takes place simultaneously with the placing of the concrete. It is used to repair damaged steel, wood, or concrete structures and to concrete areas that are inaccessible concerning practicality and cost.
21. High-strength Concrete
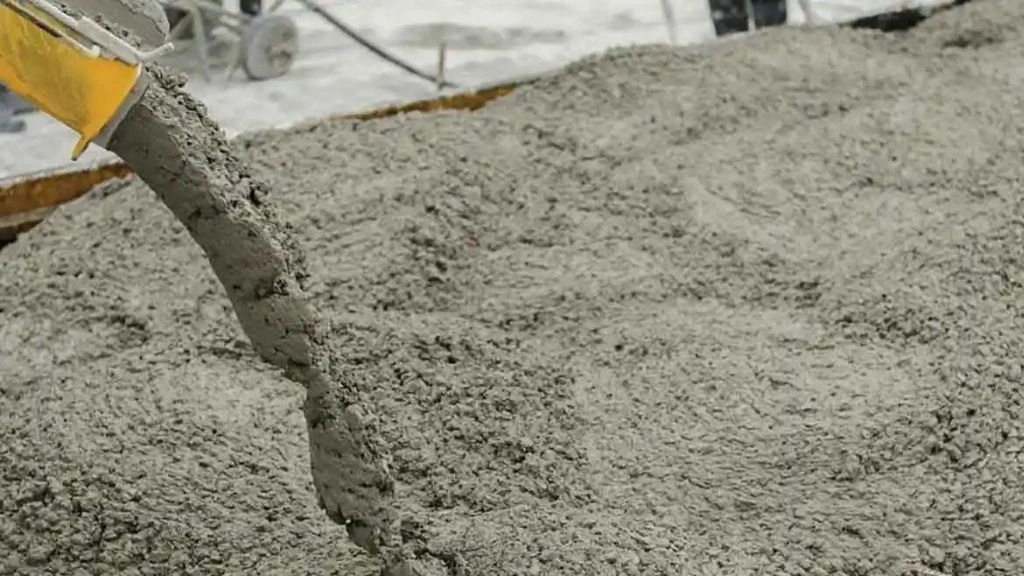
High-strength concrete is characterized by a compressive strength exceeding 40 megapascals (40MPa), which represents the tensile strength of the concrete. Concrete mixes meeting or surpassing this threshold exhibit the capacity to endure significantly more stress and pressure when compared to those with strengths of 20MPa or 30MPa.
This particular type of concrete displays resilience in the face of challenging conditions, resisting shearing, cracking, or breaking. The heightened strength is achieved by minimizing the water-cement ratio to a lower level.
High-strength concrete exceeding 40MPa finds frequent application in civil and commercial construction contexts, encompassing projects such as buildings, infrastructure, structural beams, columns, load-bearing walls, and any scenario demanding elevated capacity and durability.
22. High-Performance Concrete
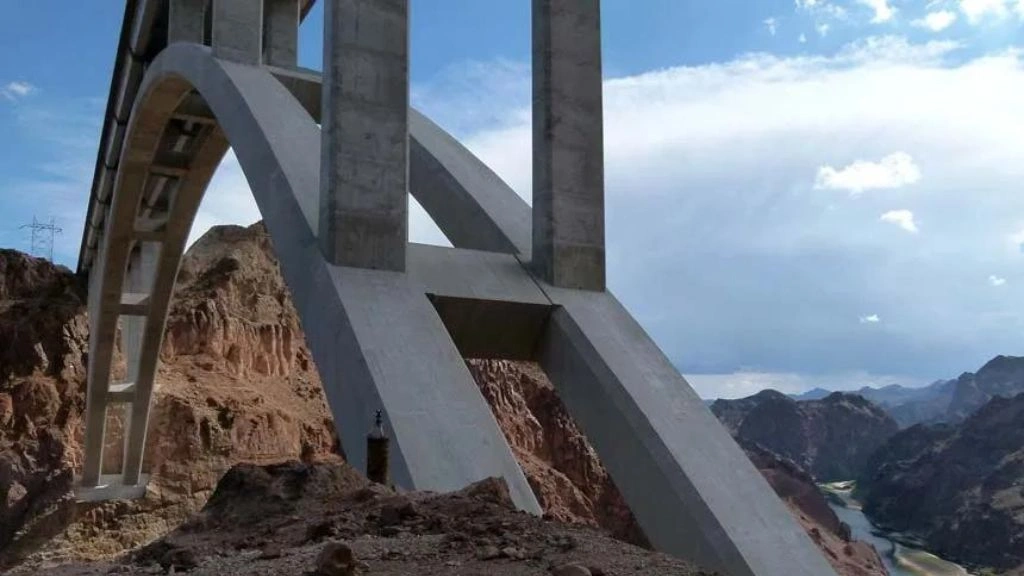
While all high-strength concrete can be classified as high-performance, it’s essential to note that not all high-performance concrete (HPC) necessarily falls into the high-strength category. High-performance concrete, or HPC, adheres to specific efficiency standards, including criteria such as ease of placement, heat of hydration, environmental considerations, longevity, durability, life-term mechanical properties, early age strength gain, toughness, and factors related to permeability and density.
It’s important to recognize that, in certain situations, HPC may have limitations in terms of strength, and this variation depends on the specific application for which it is intended.
The Bottom Line
At the end of this exhaustive list of the different types of concrete, you will find that each type is of significant importance with respect to its make and use. Concrete is something that you see everywhere around you and to satisfy your curiosity we have curated all these different types. Happy learning!