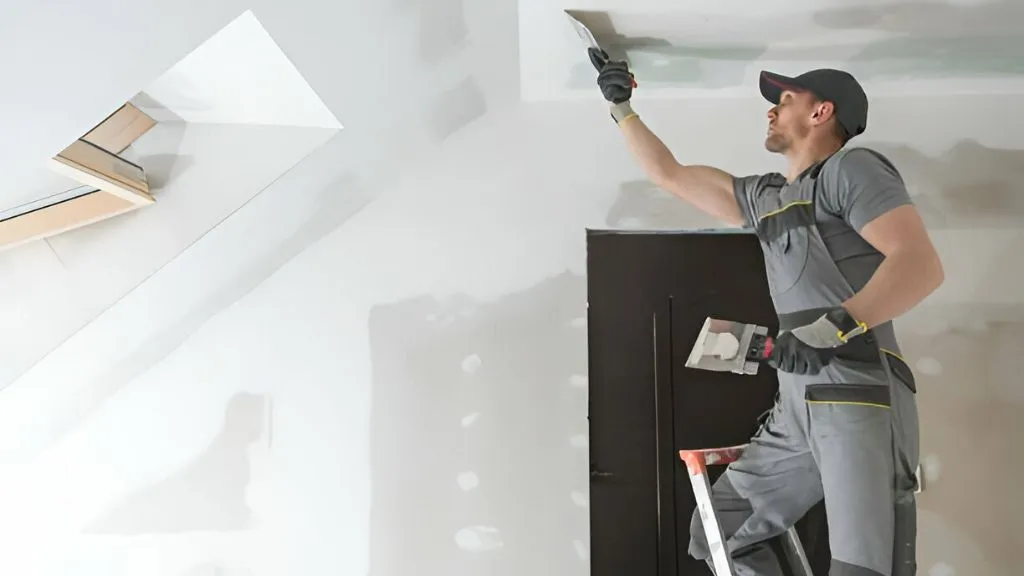
Plastering is a crucial step in construction, providing walls and ceilings with a smooth finish and enhancing their durability. However, improper plastering can lead to issues like cracks, uneven surfaces, or poor adhesion, compromising the structure’s aesthetics and longevity.
Such problems often stem from neglecting essential precautions during the process. But by understanding the right techniques and safety measures, you can achieve flawless results.
In this guide, we’ll explore the different types of plastering work in India and the precautions necessary for flawless execution.
Plastering Work: Standard Specifications of Brick Wall
A collection of plastering job specifications for various countries and locations is provided below.
Application of Portland Cement-Based Plaster Standard Specification (ASTM C926) is an American standard.
- Standardization in Europe: Rendering and plastering mortar, Specification BS EN 998-1 for masonry mortar
BIS codes (Indian Standard):
- IS 383 is a concrete specification standard for naturally produced coarse and fine particles.
- IS 1542 is a plaster sand specification standard.
- IS 2645 is an international standard that specifies the properties of integral cement waterproofing compounds.
- IS 8112 specification for 43 grade OPC.
- The specification for 33 grade OPC is IS 269.
- Cement Specification IS 1489 Portland Pozzolana
The plastering material must be tested in accordance with the manufacturer’s guidelines. Organic pollutants, silt content, sand particle size, and sand bulking should all be investigated. Sand from a river passing through a plane region is not suitable for building since it falls within the boundaries of grading zone IV.
Plastering in Construction
Plastering is a term that refers to both interior and external procedures. Plastering in construction is done differently depending on whether the walls are exterior or interior. The exterior plastering job makes the surface watertight. The internal plastering will provide a flat surface for painting. These provide aesthetically pleasant outcomes. When numerous coats of plaster must be applied to the wall surface, a single thick coat will sag owing to weight.
As a consequence, thick plastering is placed in two to three coats if necessary. For super finish coats and exterior cement plastering, two coatings are used. The first layer is referred to as the foundation coat or rendering coat. The finishing coat is the second or final coat. Three coats of lime plaster will be applied. The first coat is known as the rendering coat, the second as the floating coat, and the third and final as the finishing coat.
The Procedure of Plastering Work
1. Surface Preparation for Plastering
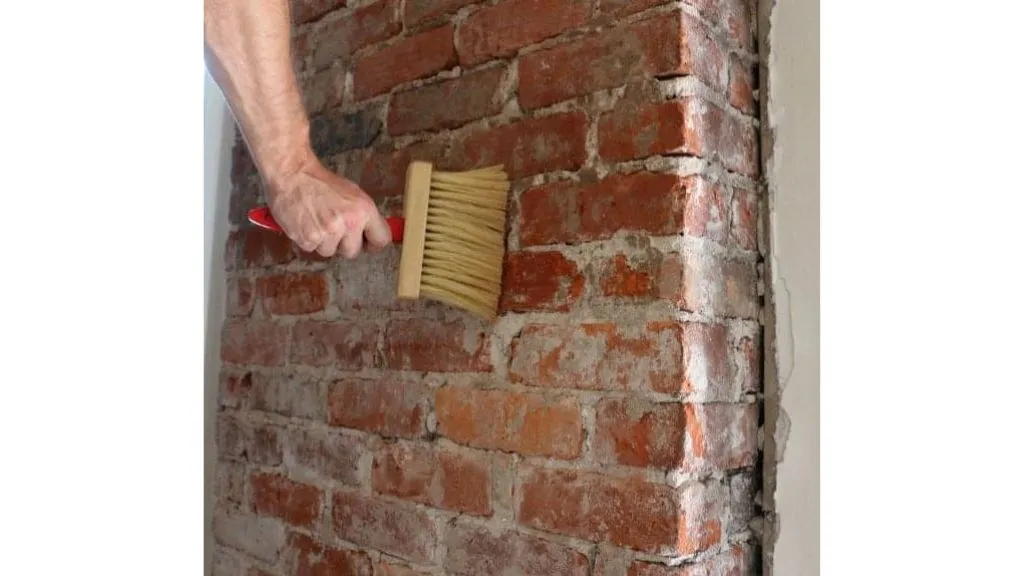
- Make all the wall’s mortar joints rough to provide a proper bonding to hold plaster.
- Roughen up the whole plastered wall.
- Clean all of the wall’s joints and surfaces using a wire brush; there should be no oil, grease, or other residues on the wall surface.
- Fill any cavities or holes on the surface with the appropriate material ahead of time.
- Rake out the mortar joint to a depth of at least 12 mm to increase bonding with the plaster if the surface is smooth or the wall to be plastered is old.
- Before laying cement plaster, wash the mortar joints and the entire plastered wall for at least 6 hours.
- If the protrusion on the wall surface is greater than 12 mm, knock it off to achieve a uniform wall surface.
2. Laying the Groundwork for Plastering
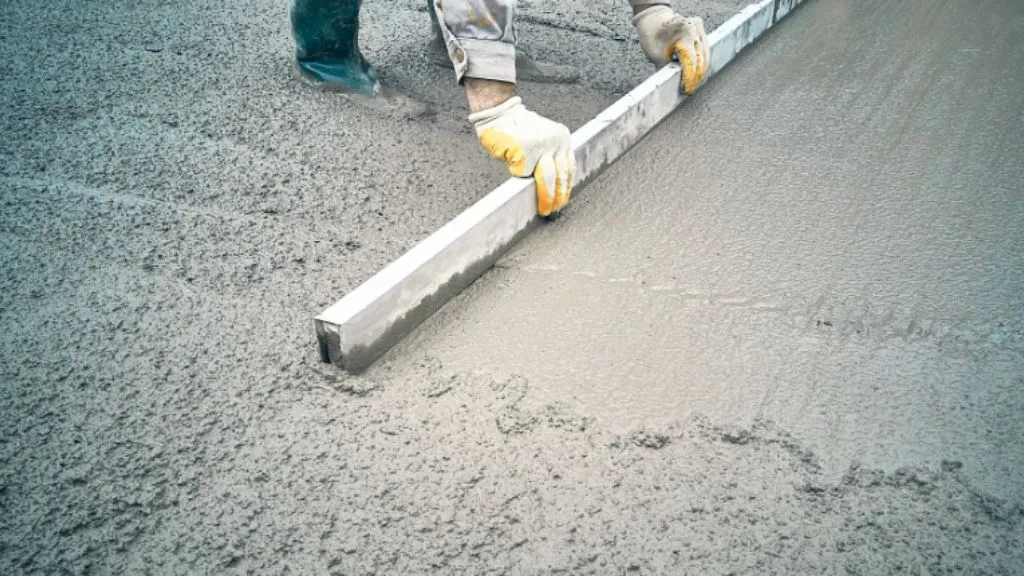
- First, attempt to attach the dots on the wall to get a consistent thickness of plastering on the surface of the wall. A dot in this context is a patch of plaster 15 mm 15 mm in size and 10 mm thick.
- Dots are fastened to the wall at approximately 2 metre intervals, first horizontally and then vertically, covering the whole wall surface.
- Using a plumb-bob, check the verticality of the dots one over the other.
- After the dots have been secured, vertical strips of plaster known as screeds are applied in between them. These screeds serve as gauges to ensure that the plastering is applied evenly.
3. Base Coat
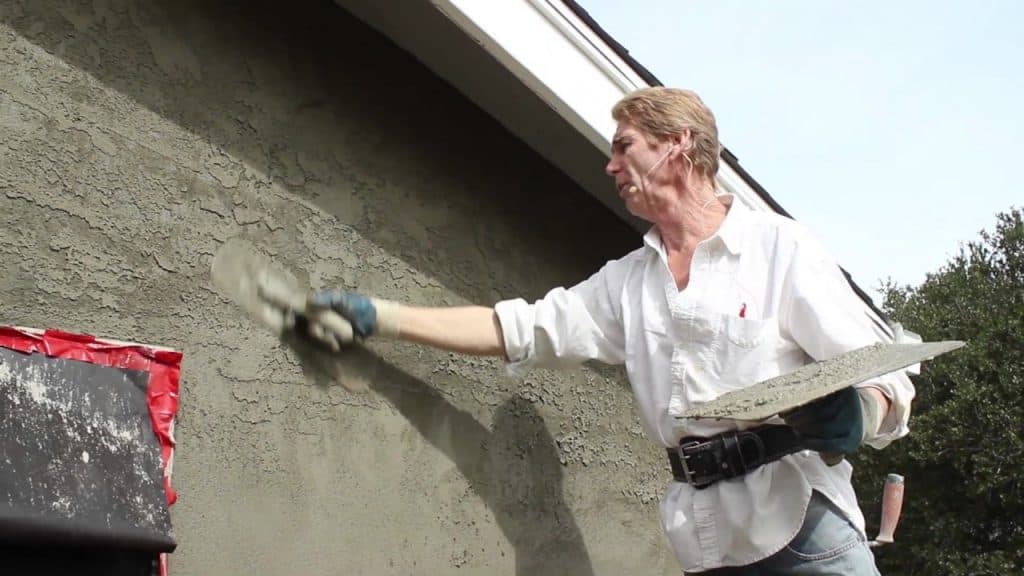
- The thickness of the initial layer plaster in brick masonry is normally 12 mm, whereas in concrete masonry, the thickness ranges from 9 to 15 mm.
- For first coat plaster, the cement-to-sand ratio ranges from 1:3 to 1:6.
- Apply the initial coat of plaster on the wall surface between the screed fissures.
- The trowel is used for this.
- Using flat wooden floats and straight wooden edges, level the surface.
- Allow the first coat to set but not dry after levelling, and then roughen it with a scratching instrument to produce a key to the second coat of plaster.
4. Finishing Coat
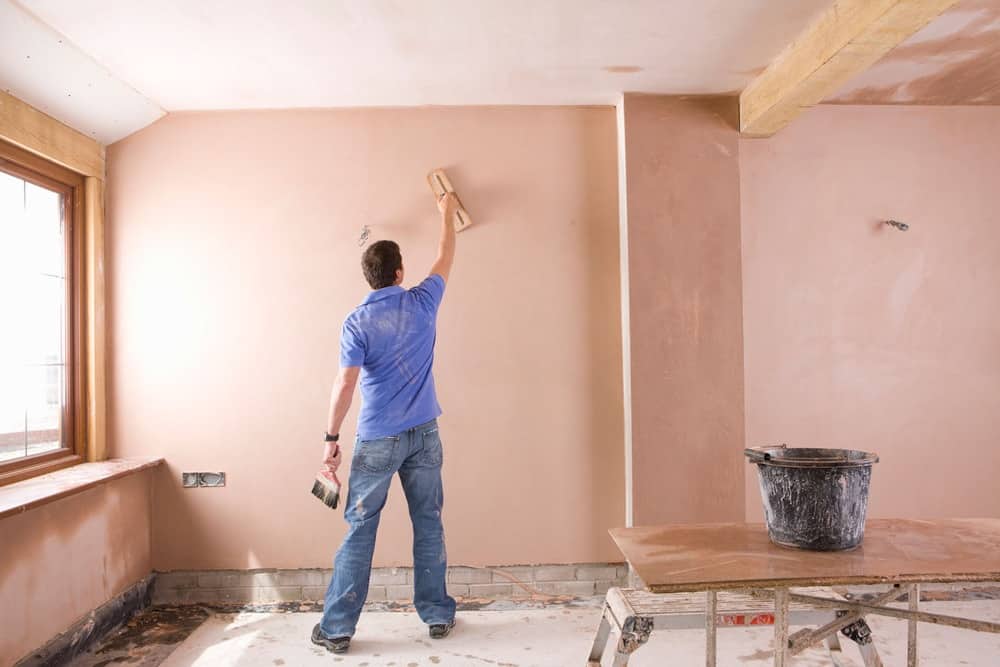
- The density of the second or finishing layer might range between 2 and 3 mm.
- The cement-to-sand ratio for the second layer plaster ranges from 1:4 to 1:6.
- Before applying the second layer, dampen the first coat evenly.
- Finish with a steel trowel after applying the last layer with wooden floats to a genuine even surface.
- To avoid connecting marks, the finishing coat should be applied from the top to the bottom in a single operation.
5. Plastering Work Curing
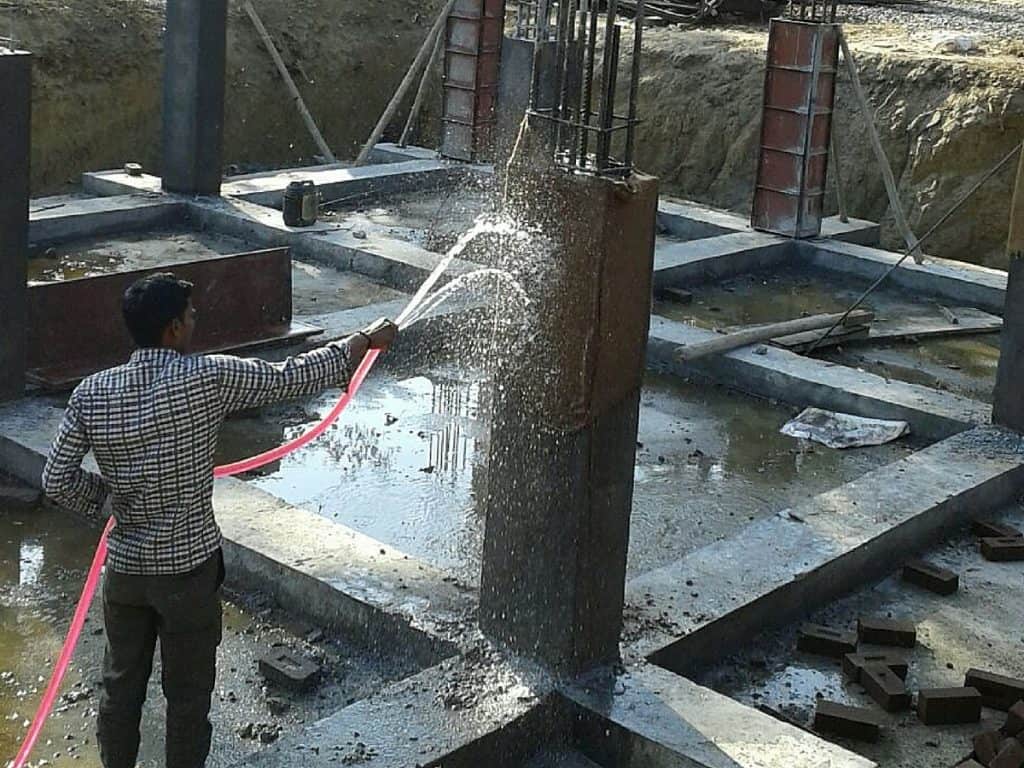
- After the plastering project is finished, it is kept moist by spraying water on it for at least 7 days in order to create strength and hardness.
- In exterior works, gunny bags or other materials are utilised to keep the plastering moist.
- Improper curing can cause cracks or efflorescence in plastering work.
What Comes after Plastering Work?
- It is critical to clean the doors or frames, as well as the floor area, after working.
- Curing should begin as soon as the plaster has properly hardened and should be completed within 7 days.
Curing begins 24 hours after the plaster is applied.
Scaffolding for Plastering Work (Steel/Wooden): Precautions
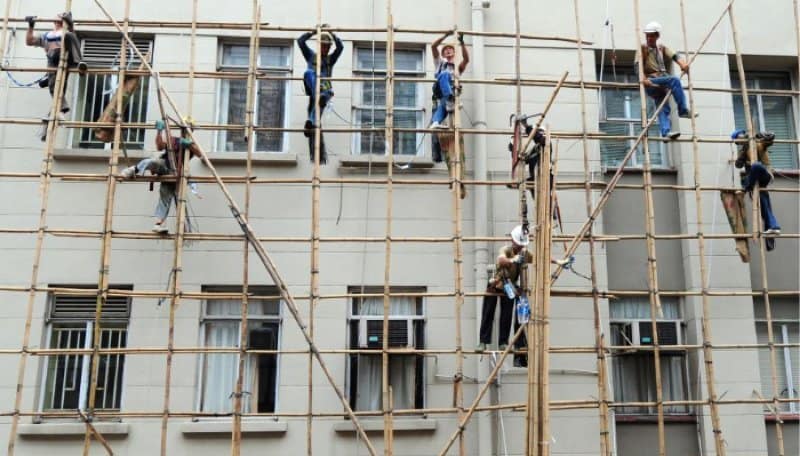
To fit specific site requirements, double steel scaffolding should be built that is sturdy enough to withstand any loads that may be encountered. It needs to be self-contained and have two sets of vertical supports.
Precautions for Plastering Work that Incorporates Services
HVAC, electrical conduit, and plumbing lines, as well as suitable finishing, must be installed. Any grooves and sleeves depicted in the drawing should be finished in the right line, level, and position, or in accordance with the engineer’s directions. The scaffolding sleeves must be carefully polished and cured. It will aid in reducing the structure’s leakage problem.
Precautions during the Workmanship of Plastering Work
- The plastering work must begin with proper surface preparation. The brick wall junction should be racked out appropriately. Brushing and scraping should be used to remove dust and loose mortar. Before plastering, the surface should be carefully cleansed with water, cleaned, and kept moist.
- A sieve should be used to filter the sand, and the cement mortar should be proportioned according to the specifications.
- Mortar should be utilised soon after it has been mixed, and large volumes of mortar should not be mixed at once. It must be used within 30 minutes after adding water.
- To avoid cracks, a 150 mm wide chicken mesh should be installed between the connection of the column/beam and the wall. Nails measuring 150 mm centre to centre must be used to secure chicken mesh.
- The amount of cement applied for the floating coat in the case of internal cement plaster with a floating coat of neat cement must be 1 Kg per Sqm.
- Exterior plaster with a thickness of 18 mm must be applied in two coats. The initial 12mm thick layer should be left rough and furrowed 2 mm deep with a scratching instrument before applying a 6mm thick second layer.
- Finish the surface true using a trowel and a wooden float to get a smooth surface.
- As the work continues, it should be examined often with a true straight edge no less than 2.5 m long and plumb bobs. Always double-check the vertical or horizontal surface’s line, level, and plumb.
How to Check the Quality of Plastering Work?
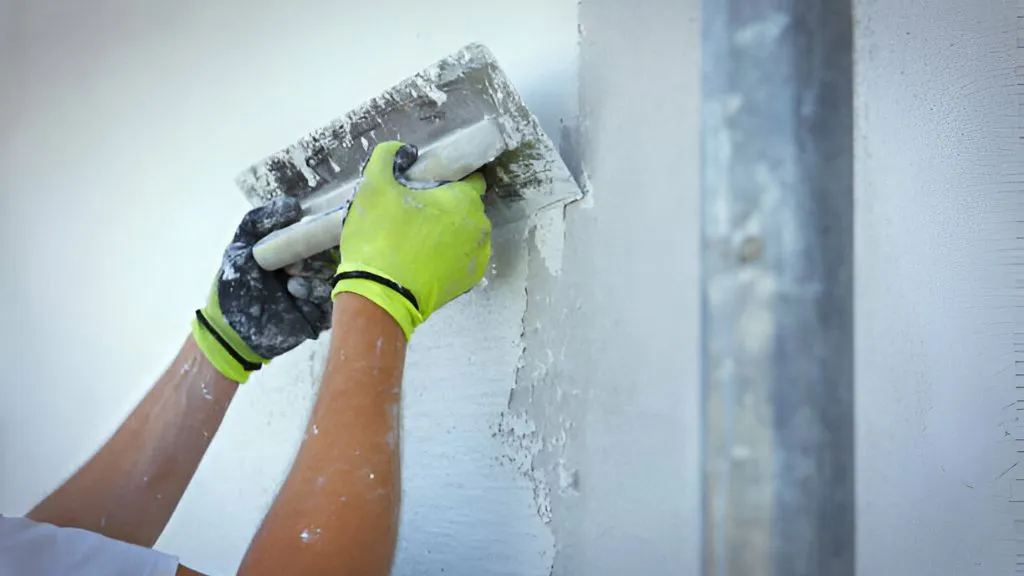
- Before beginning the plastering, the surface must be well prepared.
- The plaster materials used should meet IS regulations, and the water-cement ratio should be tested.
- Checking the level marks is essential. Make level marks with new mortar on all four walls. As a result, after plastering, the room size is truly square or entirely rectangular. Otherwise, placing tiles for the floor would be tough, and the result will be unappealing.
- Smooth surfaces and straight edges should be verified.
- Ensuring that even when we locate holes in masonry for conduit pipes, they are fixed with cement mortar and properly cured.
- Holes for scaffolding should also be properly sealed and cured, since they are a major source of leakage or moisture in the wall, and curing at such a position is frequently overlooked.
Safety Precautions Taken During Plastering Work
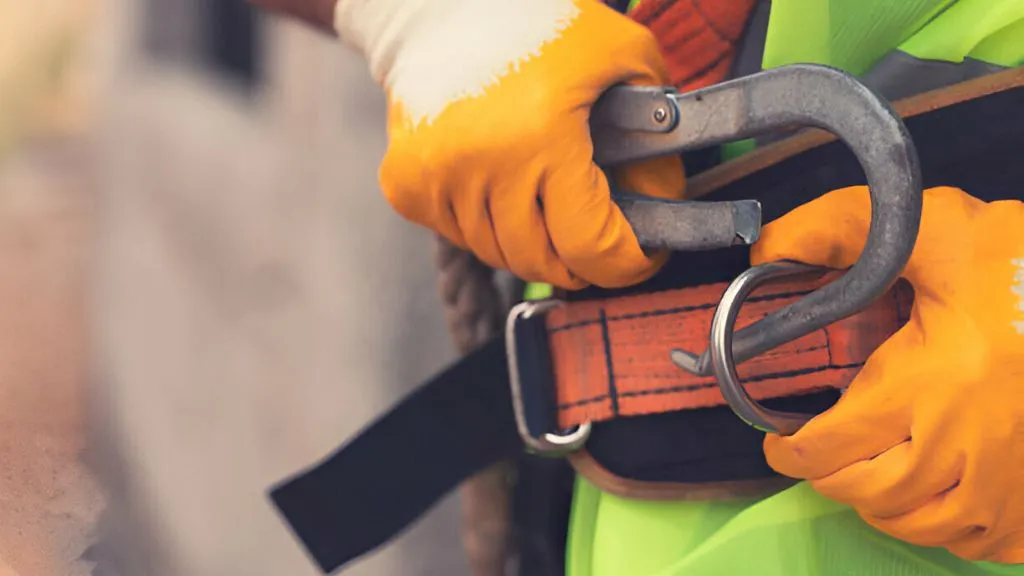
- Material handling, placement, and cleaning method statements must be developed and followed.
- When handling work, personal protective equipment such as a safety helmet, safety belt, rubber hand gloves, goggles, facemask, and rubber shoes should be used, and a first-aid kit should be readily available.
- When working in a tight and dark location, proper ventilation and electric lighting must be given.
- The material transportation machine’s calibration should be reviewed on a regular basis. Any fault or flaw on the computer should be addressed as soon as possible. The machine operator must have recognised the agency’s licencing.
- It is critical to keep the room clean and the supplies in excellent shape. Material waste should be collected as soon as possible from the site.
Waste management for Plastering Work
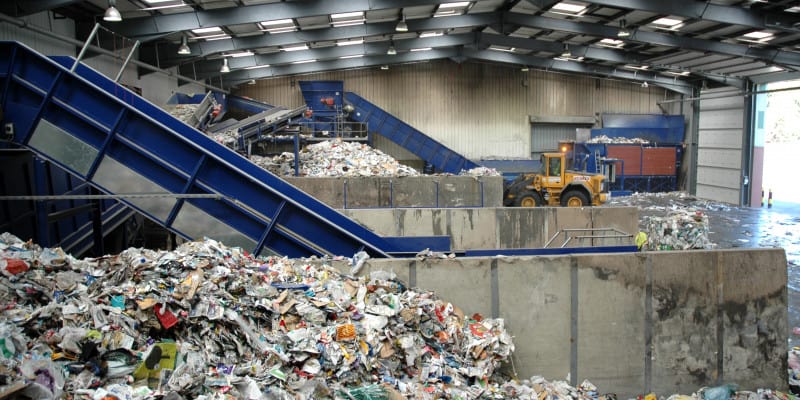
Waste may be minimised by employing appropriate building procedures. Regular on-site waste management training should be planned. Waste products should be kept in a secure location and repurposed or recycled wherever feasible.
Measuring Plastering Work in Construction
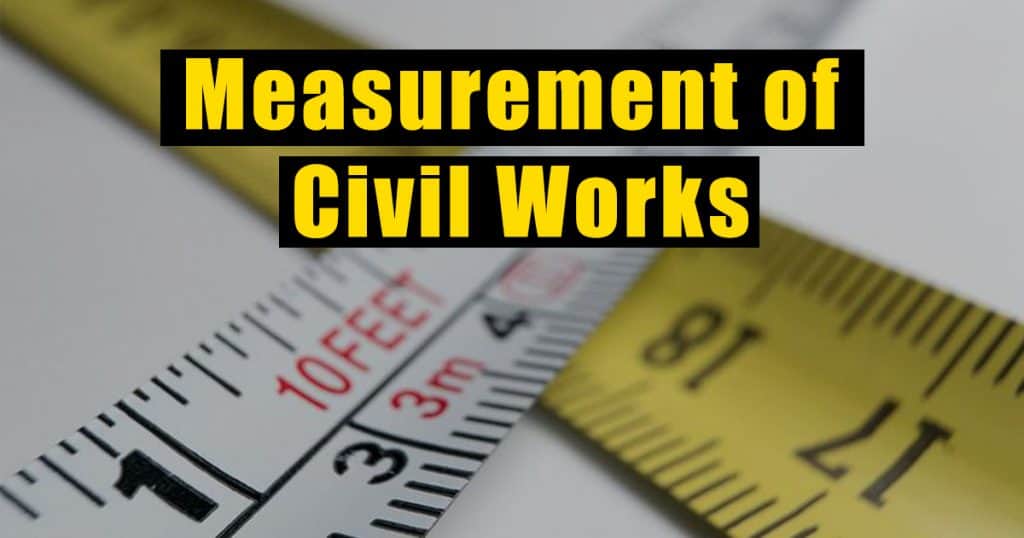
According to IS 1200 – 1976, dimensions should be recorded to the nearest 0.01 m, and areas should be calculated to the nearest 0.01 m2 (Method of measurement of building and civil engineering work P-XII, Plastering and pointing). The length of plaster shall be measured between the brick walls or brick partitions (before the plaster is measured), and the height of plaster shall be measured from the top of the floor or skirting to the ceiling.
The provision of IS Code: 1200 – 1976 governs the deduction of door/window/ventilation, etc.
Plastering procedures are developed by the plasterer depending on the precautions outlined above. It will help them manage the plastering worker. It will also help them finish the plasterwork on schedule. To properly connect with the plasterer, the homeowner must be informed of all plastering work guidelines. If the homeowner learns all of the above-mentioned plastering work recommendations, they will be rewarded for their efforts by obtaining high-quality plasterwork.
A Good Plaster’s Requirements
The following are the essential requirements for a good plaster:
- A good plaster mixture must cling to the surface under all weather conditions.
- It must be both inexpensive and economical.
- The plaster must be tough and long-lasting.
- The plaster mixture must be usable in all weather conditions.
- Plaster must evaluate and avoid the entry of moisture content penetration from surfaces.
- The plaster must be sufficiently workable to allow for the necessary application.
Types Of Plastering in Construction

1. Lime
Plastering of lime is the technique of coating varying amounts of lime mortar on building surfaces or any other structural surface. The type of project, as well as the number of coats to be applied, will decide these proportions.
2. Cement
As it’s easy to execute, cement plaster is a great choice for outdoor plastering. It is most commonly used on damp-prone surfaces such as reservoirs, water tanks, copings, floors, and bathrooms. In these areas, non-absorbent surfaces are mainly required. When the required thickness reaches 15mm, two coatings of cement plaster are applied.
3. Mud
Plastering of mud is the most cost-effective method of plastering. This is used in the construction of village houses, temporary constructions, as well as shelters These are inexpensive and offer excellent heat insulation characteristics. This will help to create a more pleasant living environment.
Conclusion :
During your home’s construction, plastering makes the rough surfaces of the walls smooth. Plastering work covers rough edges and uneven surfaces, thus increasing durability and strengthening walls. Plastering work also gives a good finish to the walls of your house and this will make your home look appealing. Plastering in construction provides you with better longevity. After the plastering process is completed, the walls will become extremely sturdy. They can protect your walls from humidity, heat, rain, and other climate factors. Therefore, it’s highly imperative that Plastering in construction is implemented when you’re planning to build your dream home to provide strength and durability to your walls.