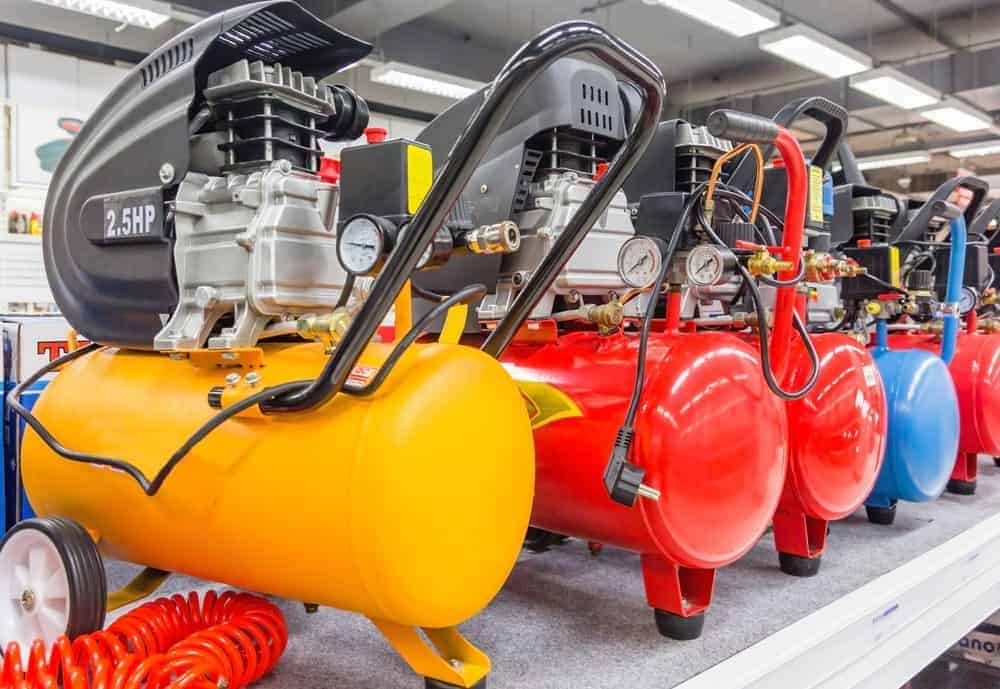
Compressors are one of the essential elements in industrial sites as they offer easy support to heavy-duty operations. It is necessary to choose the most appropriate Type of Air Compressor to provide a useful source of electricity for the tools.
What Is An Air Compressor ?
The types of compressor refers to a machine used in industries to convert one type of energy into another that can be stored and eventually used later. Different types of Air compressors are powered using diesel, gas engines, and electric motors.
Given that they may be utilized as a power source for electric tools, air compressors are some of the most essential equipment found at construction sites. There are several varieties of air compressors, each with certain advantages and disadvantages.
Based on their internal processes, air compressors can be classified as positive displacement or dynamic displacement. The four most typical types of air compressors are as follows:
- Rotary Screw Compressors
- Reciprocating Air Compressors
- Axial Compressors
- Centrifugal Compressors
Below, we’ll go through the main characteristics of each kind and describe how each one functions to help you make an informed selection for your project.
What Are The Types Of Compressors ?
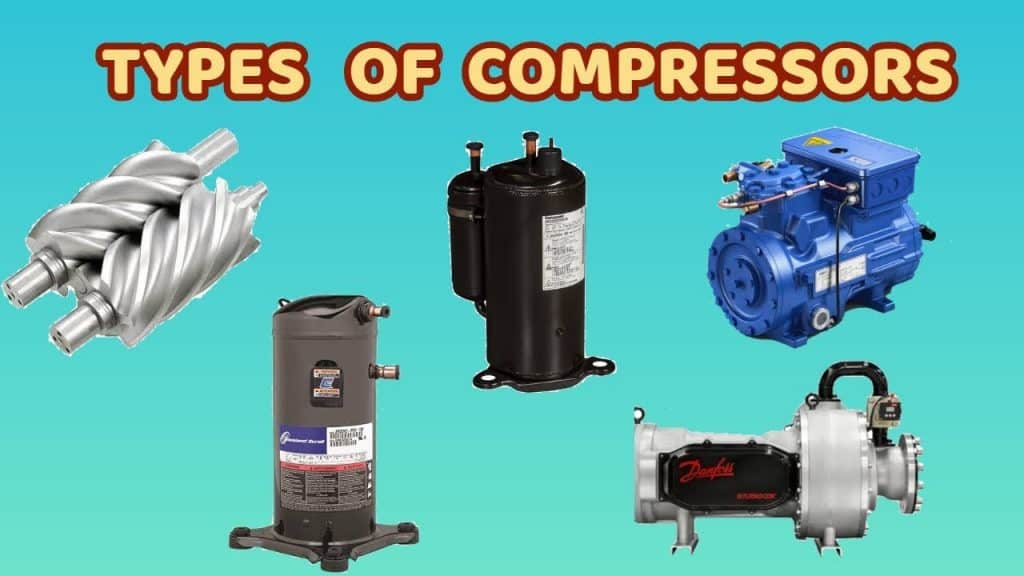
Classification of compression Depending on the types of compression, may be positive displacement or dynamic displacement.
Nonetheless, in the industrial sectors, some of the most common types of compressors that are used include the following:
1. Positive Displacement Compressor

This type of compressor can generate power using air displacement. These air compressors have different internal working mechanisms, but the working principle remains the same for almost all compressors.
The compressor has a cavity responsible for holding air carried from outside. The cavity in the machine responsible for storing is brought from outside which is then compressed to increase the potential energy and air pressure.
2. Reciprocating Compressors
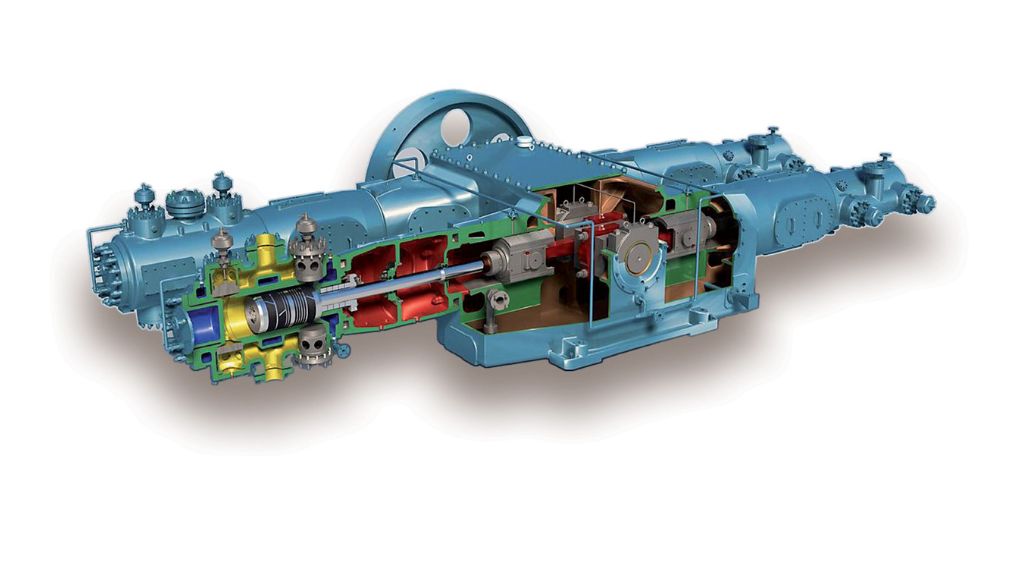
Reciprocating compressors are one of the most popular types of displacement compressors. These compressors are mostly used in small work sites such as home construction or garage.
These might not be eligible for working continuously, however, their moving parts are usually more numerous and are thoroughly lubricated by the use of oil to ensure proper movement. This is why most domestic refrigerators make use of reciprocating compressors.
These types of air compressors have a piston within the cylinder that is responsible for compressing and displacing air for building pressure. Unlike other compressors- these are usually available in different variations such as multi-stage and single-stage.
Multi-Stage Compressors
- The multi-stage compressors are handy for providing a large amount of power on the go. The multi-stage compressors can be handy for conducting intense functions such as maintenance and assembly as they can reach up to 30 horsepower.
Single-Stage Compressors
- The single-stage compressors are efficient for smaller projects such as metalworking, woodworking, and more.
3. Rotary Screw Compressor
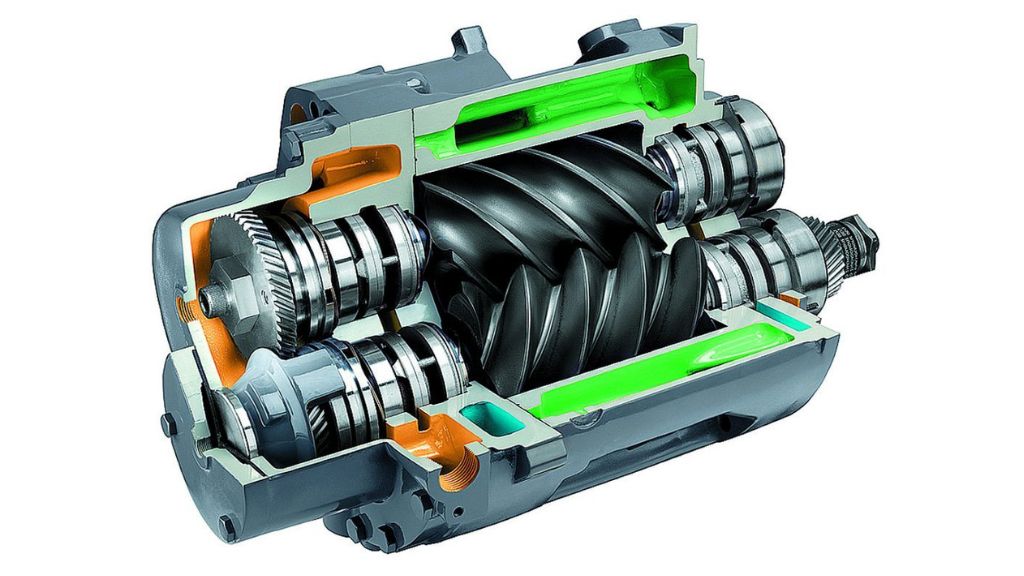
Rotary screw compressors are one of the most commonly used compressors because they don’t require extensive maintenance and have an internal cooling system.
The rotary screw types of compressors are large compressors that can either run oil-free or be lubricated using oil. The compressors have two internal rotors responsible for generating energy within these. The pressure builds up when the air gets trapped between the opposing rotors.
It features an internal cooling system that can function within a range of 5 horsepower to 350 horsepower.
The rotary screw compressors are further divided into two types of screws:
Dry Type Rotary Screw
- In a dry-type rotary compressor, the intermeshing rotors will not be responsible for contacting one another. The relative clearances within the compressor are maintained to offer close tolerances for promoting external lubricated timing gears.
- The presence of an intercooler and aftercooler contributes to dual-stage compression. The coolers are lubricant-free rotary screw compressors whose range can easily vary from 25 to 1200 HP.
Lubricant Injected Rotary Screw
- These types of compressors are most efficient for industrial use. In a lubricant Injected Rotary screw, the lubricant will either have a composition of hydrocarbon or synthetic material.
- The mixture of lubricated injection with compressed air is made to pass through a sump in which the compressed air and lubricant are obtained as two different entities. The speed and directional change of the liquid helps in maximum separation. The separator elements help in the further removal of the remaining aerosol.
- The compressor usually features two stages. The lower internal loss and interstate cooling help lower the pressure in each stage, thereby promoting compression efficiency. As a result, the system will need less energy for air compression in the final stage.
4. Dynamic Compressors
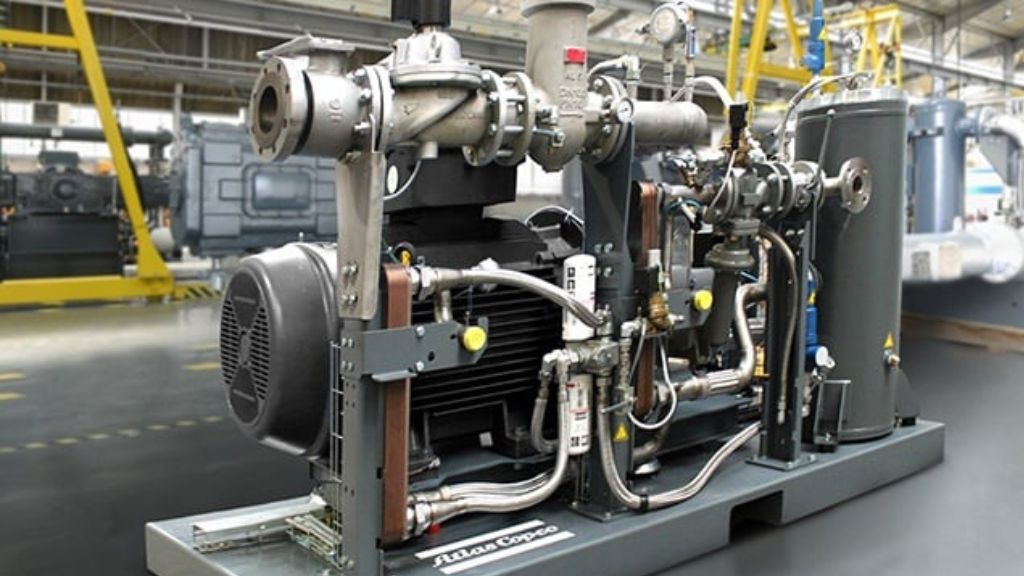
The dynamic compressors are further of two types- axial and centrifugal. These types of compressors are responsible for generating horsepower as they draw air into the fast-rotating blades and then restrict the airflow to generate pressure. The kinetic energy is stored in a static form in a dynamic air compressor.
Axial Compressors
- Axial compressors may not be helpful for industrial projects but can be efficient for high-speed planes, ships, and engines. Comparatively, the efficiency rate of these is pretty high, and so is their price.
- The axial compressors are capable of generating thousands of horsepower. Therefore, these are mainly used for aerospace research purposes.
Centrifugal compressors
- Used mostly in large-scale manufacturing plants, centrifugal compressors can be extremely efficient. These compressors are responsible for slowing and cooling the incoming air using a diffuser, and furthermore , these are responsible for building the potential energy.
- The compressors follow a multi-phase compression process that helps them generate a high amount of compression in a small machine. Unlike other compressors, these do not require a lot of maintenance and can produce oil-free air.
- The centrifugal compressors are handy for construction sites like steel manufacturing or chemical plants. Furthermore, these are capable of reaching up to 1000 horsepower. Again, the domestic refrigerator uses the following type-wise of compressor: scroll compressors.
5. Fixed Speed And Variable Speed Compressors
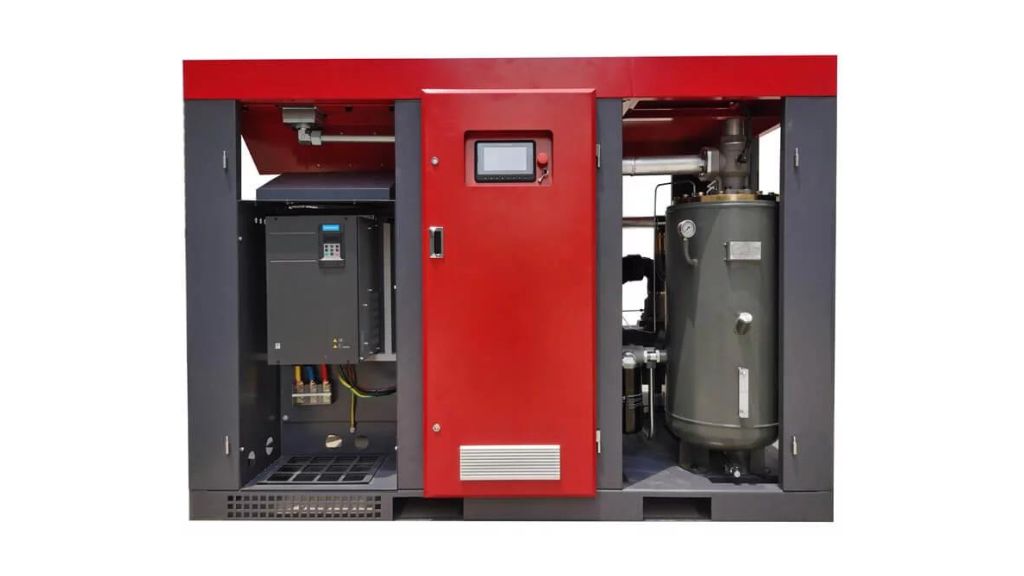
Fixed-speed compressors run at a specific speed that can operate completely when the motor is in a running phase and the air is being compressed. However, it may become inefficient if the unit unloads. After a certain point, the compressor will spot functioning.
On the other, a variable-speed compressor can help turn the motor into a specific amount of air. The speed of the motor usually depends on the demand of the device. In a variable-speed compressor, there is significantly less chance of energy wastage.
Whenever using these types of compressors, it is advisable to conduct an air usage audit. The audit will play an essential role in understanding the energy consumption by each of these.
How To Choose The Most Appropriate Air Compressor?
different types of Air compressors are power-generating machines that can be extremely handy in the long run. These can help to determine the energy output level. However, if you are purchasing these for industrial purposes, you will need to consider the following:
1. The Air Quality Of Oil-Free Compressors
Whenever you choose oil-free compressors, you need to check the air quality. The oil-powered air compressors may not be handy if the compressor is being purchased for a clean manufacturing environment.
The air compressors mostly use oil for lubrication, creating fumes and contaminating the air, thereby hampering the entire manufacturing process. However, using an oil-free compressor in the manufacturing environment can help to reduce the risk.
Comparatively, the oil-free compressors are expensive, but they offer proper cleaning. A small amount of oil will be helpful for machine lubrication. The running cost for oil-free compressors is usually low because the parts do not require constant maintenance.
2. Energy Efficiency
Long construction projects require energy efficiency, and it is necessary to use energy-efficient compressors that can be worthwhile in the long run. Natural gas compressors can be effective for functioning with different equipment and tools.
These tend to run more efficiently than others and easily manage the partial load. Comparatively, the natural gas air compressors can function more efficiently even with partial loads. The heat recovery capabilities of the same are usually higher than the electric compressors.
3. Focus On Portability Limitation
If you need to move the compressor across different sites, you must choose a portable compressor. There are small and lightweight units that are available in compact packaging.
These compact units aren’t as powerful as large units and can only be efficient for small projects. These units can also be plugged within the car adapter to use an airbrush painting or tire inflation tool.
4. Do You Need Extra Features?
Many air compressors are available in the market with extra features. You need to determine whether you need these or not. Most air compressors feature thermal protection to determine the internal heating and prevent motor damage. Many air compressors also sport a belt-drive system that can be efficient for quiet operation.
Final Words
The types of compressors are used for responsible for pumping refrigerant from the refrigeration system and every other kind has its own control system. Therefore, before purchasing one, you must determine whether you need it for a small-scale or large-scale project. Additionally, it is also advisable to check the airflow of the same.
The article above provides a thorough guide on types of compressors and how to choose one. To get the maximum value for money, you must make sure to check the small detator to make the purchase a vital one.